Are you exploring conveyor building services to enhance your material handling system? Efficiently designed and implemented conveyor solutions are key to optimising your operations. This article provides a no-nonsense look into how professional conveyor building services can tailor systems to your business needs, maximise space, and streamline workflow, covering the journey from concept to ongoing system support. With this comprehensive piece, we intend to answer your questions thoroughly without the need of additional storage space (pun intended).
Key Takeaways
- Conveyor building services encompass design, installation, maintenance, and customisation of conveyor systems, ensuring tailored solutions for various industries to optimise efficiency and use of space within their operations.
- Automated conveyor systems significantly reduce labor costs, enhance productivity, and streamline logistics by leveraging advancements in sensors, robotics, and machine intelligence, while regular maintenance is essential for longevity and performance.
- Investing in a conveyor system requires a comprehensive look at the initial outlay as well as the long-term operational savings, with life cycle cost analysis helping businesses assess the true cost of ownership and return on investment.
Understanding Conveyor Building Services
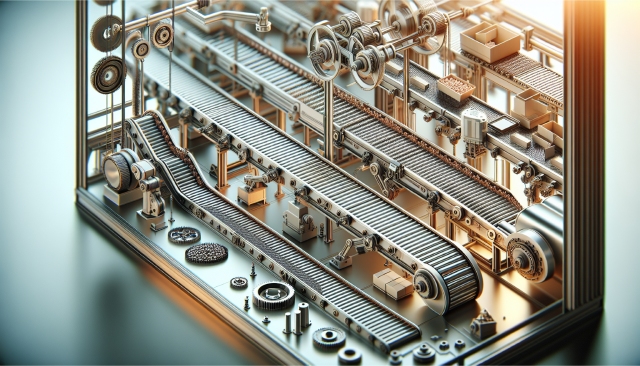
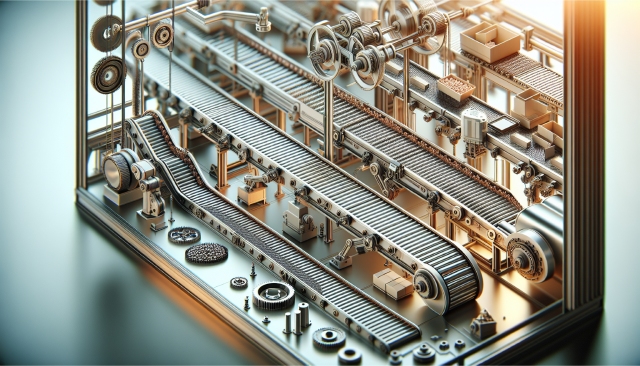
Conveyor systems are like the unsung heroes of the industrial world, making everything run smoother and faster. Picture them as the choreographers of your factory floor, designing the perfect routes for moving products efficiently and with style. They do more than just carry things from point A to point B—they bring order, consistency, and smart space management to your operations, ensuring every part of your process is firing on all cylinders.
What Happens Next?
When you strategically implement these conveyor systems, they become the reliable highways that keep your products flowing smoothly through the complexities of warehouse activities. It’s all about creating a seamless, steady rhythm that enhances productivity and keeps your business moving forward.
Defining Conveyor Building
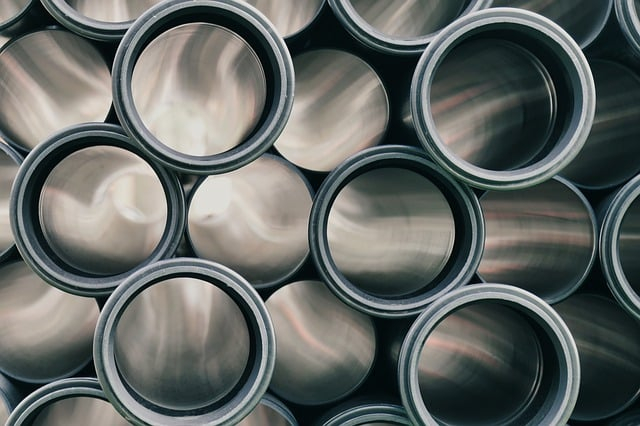
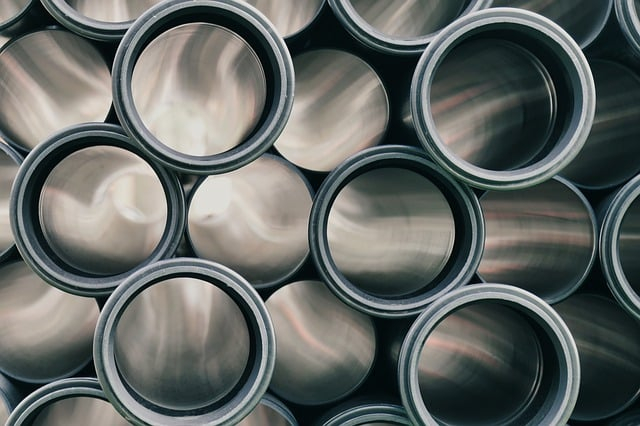
The construction of a conveyor system is an elaborate endeavour that extends beyond simply installing conveyor belts. It requires a thorough understanding and integration into the operational essence of each facility, ensuring systems are not only tailored but customised to seamlessly align with the demands of various industries and specific applications. This comprehensive approach spans from initiating assembly to executing exhaustive quality checks, involving several critical activities within conveyor building.
Critical Activities for Conveyor Building
- Conceptualising and engineering design for the system
- Choosing suitable components for conveyors
- Manufacturing and piecing together structural elements
- Proper installation and alignment procedures for belts
- Conducting rigorous testing before commissioning the full system
- Offering consistent maintenance support post-installation
By utilising expert conveyor building professionals, you can guarantee your conveying solution will be constructed adherent to stringent standards while achieving heightened levels of efficiency geared toward enhancing productivity. Careful and meticulously engineered systems will save you from unwanted costs.
The Anatomy of an Efficient Conveyor System
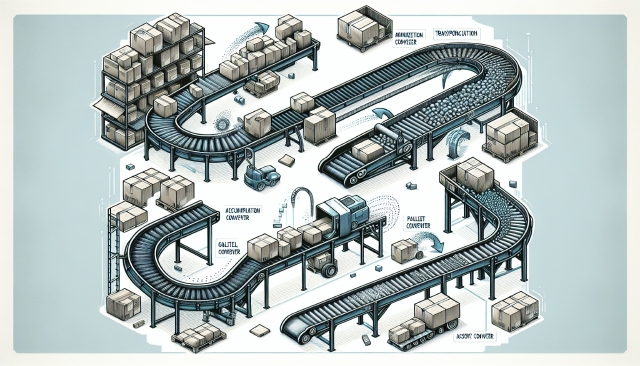
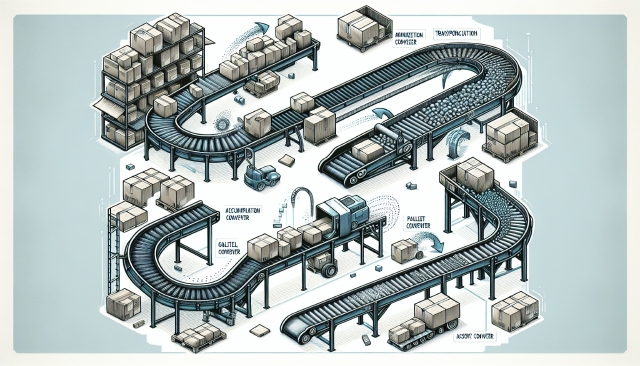
A conveyor system functions like a collation of finely tuned engineered systems, with each part critically contributing to its overall performance.
Integral Components of the Conveyor System
- Motor and gearbox: They are the driving force behind the movement of the conveyor belt.
- Rollers: These provide support for and direct the conveyor belt in a smooth fashion.
- Pulleys: Responsible for altering the direction of travel and maintaining tension on the belt.
- Guardrails: Essential for safety measures, they prevent materials from slipping off by preserving structural integrity.
Envisioning your operations as being driven by an essential current, picture your highly durable layered conveyer belts guiding vital materials along their course. Expertly designed rollers and pulleys operate harmoniously to maintain motion while guardrails offer vigilant protection, upholding both safety standards and structure.
Safety & Reviewing
To safeguard against malfunction or material mishaps that could throw it off course, regular reviews coupled with prompt upkeep act as critical safeguards for your system’s longevity. And central to all these elements is where you’ll find one motor steadily humming away — fuelling forward progression that ensures continuous business productivity.
Types of Conveyors
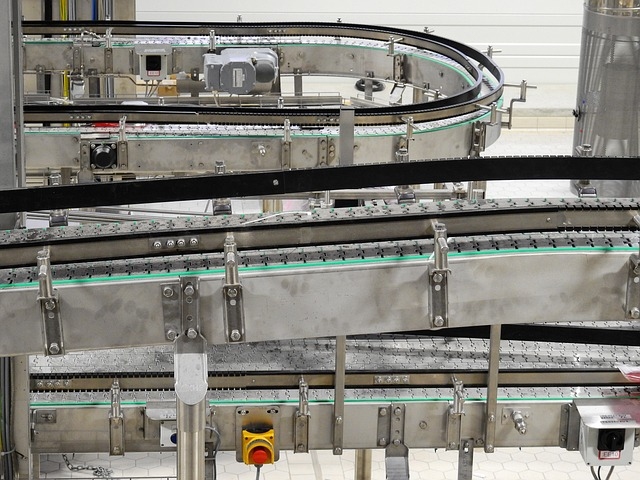
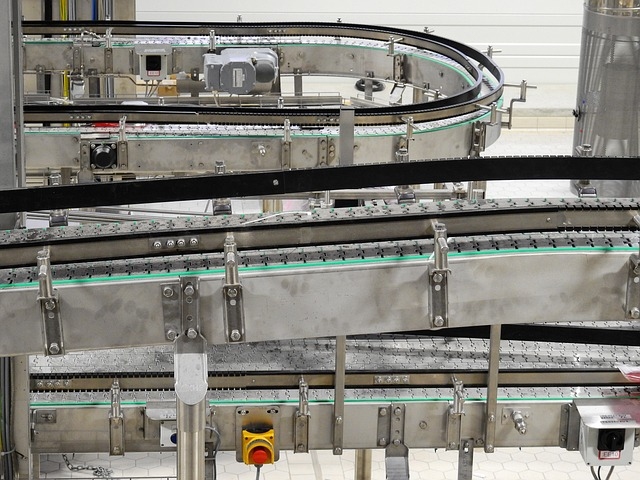
In the realm of materials handling, a wide array of conveyor types exists to fulfil the diverse requirements present in warehouse operations. Systems available include:
- Standard flat belts
- Helical spirals
- Gradient inclines
- Elevated tracks
Conveyance systems within warehouses serve as pivotal arteries, channeling products throughout the space with notable efficiency and fluidity, thereby enhancing the functionality of industrial trucks.
Categories of Conveyors
- Belt conveyors that establish an ongoing circuit for transporting parcels or bulk commodities
- Motor-driven live roller conveyors which effortlessly propel weighty items or large volumes
- Gravity-powered conveyors that utilise gravitational pull to move goods in an energy-savvy manner without resorting to electric power
These examples demonstrate the ingenious yet straightforward nature inherent in handling mechanisms designed for material transport.
Innovative Features
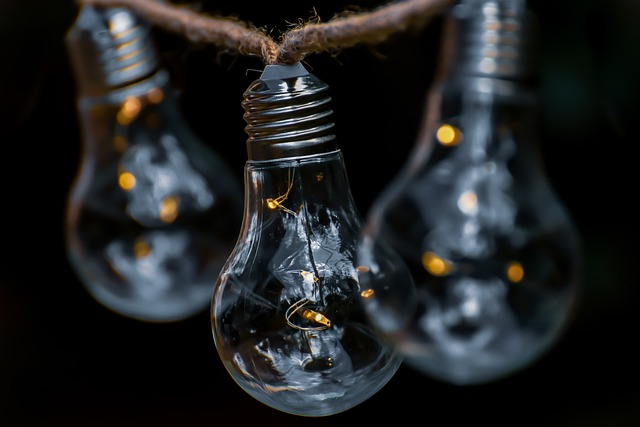
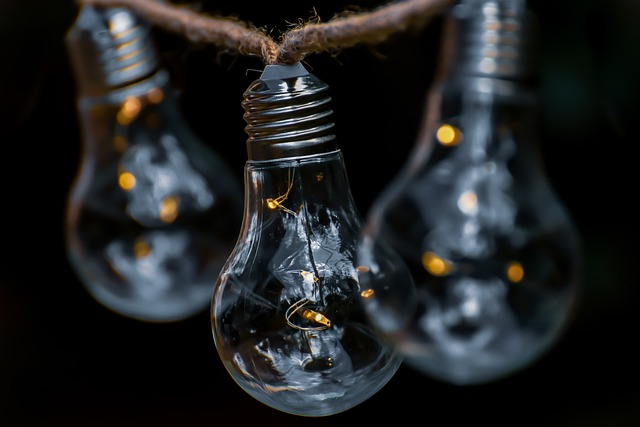
In the domain of material handling, conveyor systems are continuously evolving with advancements such as:
- Right-angle transfer conveyors that alter product trajectories to adeptly manage spatial limitations and process intricacies.
- Pallet conveyors equipped with robust rollers and chain drives capable of bearing the weight of heavy loads.
- Elevation conveyors designed to transcend vertical boundaries, thereby maximising manufacturing space utilisation.
Accumulation conveyors enhance operational efficiency by collecting and organising items for procedures like loading or labelling bulk material. This strategic innovation in both materials handling and equipment storage is pivotal for proficient management of unit loads.
Custom Conveyor Solutions for Unique Challenges
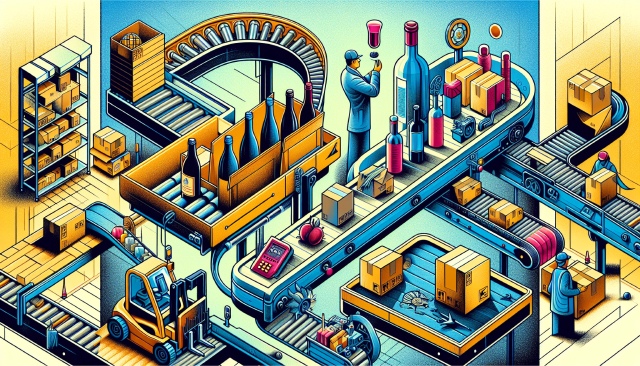
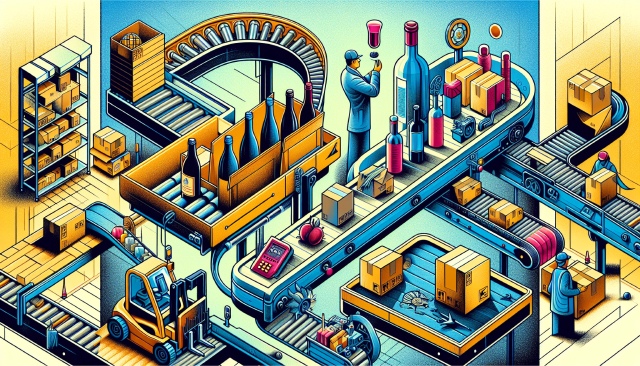
Conveyor systems are specialised tools, not universally applicable in their design. Different sectors, such as the wine and spirits industry that needs gentle handling or the fast-paced e-commerce arena, demand conveyors crafted to address specific challenges. Customised conveyor solutions cater to these individual requirements with precision, especially when grappling with constraints related to space and diverse material handling tasks. They are instrumental for optimising your company’s operational processes.
These systems boast adaptability and flexibility, incorporating advanced technologies such as voice picking and pick-to-light methods. Such innovations significantly boost efficiency and dependability within material handling workflows.
Tackling Space Constraints
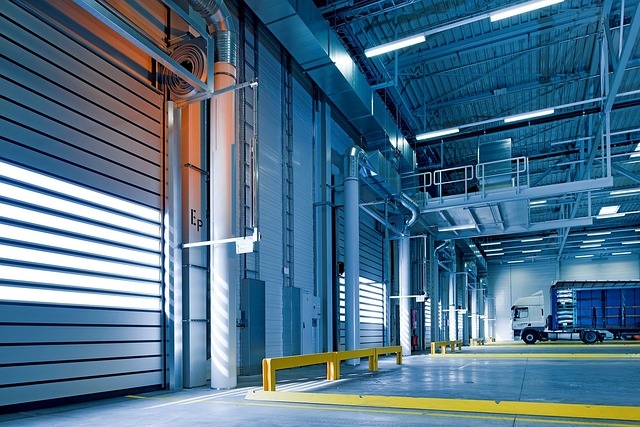
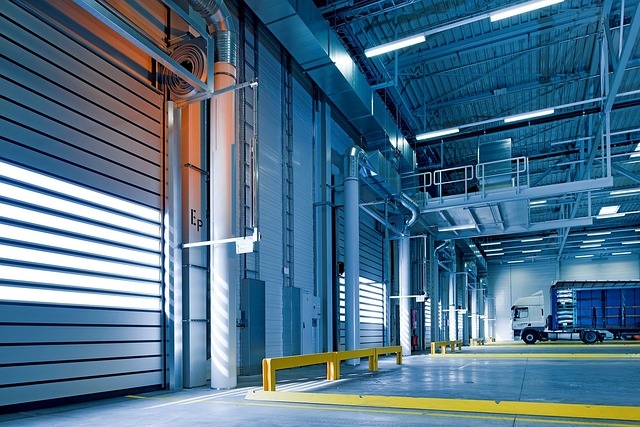
In the realm of warehouses, space is exceedingly valuable. Customized conveyors tackle this issue directly by crafting layouts that not only make the most out of available floor space but also exploit vertical storage possibilities to their maximum extent. Such designs significantly enhance equipment storage capabilities as well.
These tailor-made conveyors turn spatial constraints into openings for increased productivity and creativity, accommodating everything from bulky and massive items to configurations suited for narrow aisles.
Handling Specialised Materials
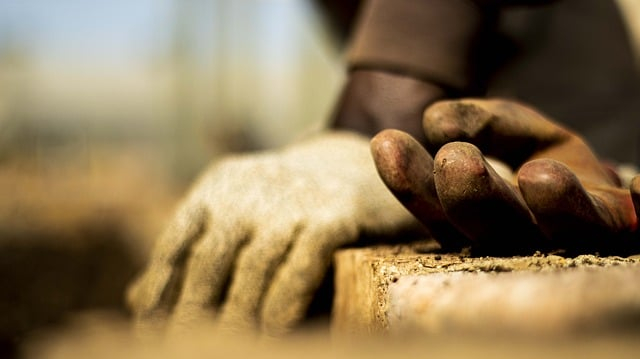
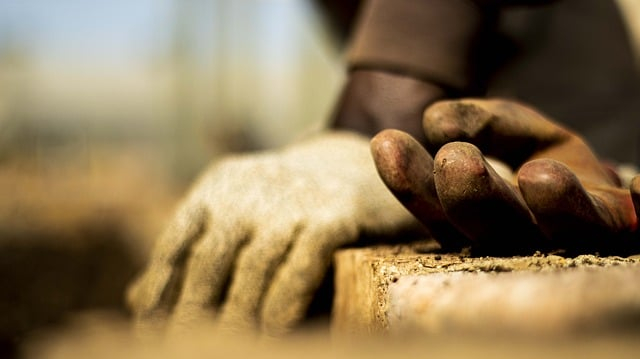
The transportation of specialised materials necessitates a unique material handling system tailored to the specific characteristics of the products it moves. In sectors such as wine and spirits, having a conveyor system specifically designed for their needs is crucial to prevent operational disruptions and logistical challenges. Automated systems play an essential role in reducing manual labor while simultaneously lowering injury risks, thereby streamlining the movement process from bulk items all the way to heavy loads with greater safety and efficiency.
Integrating ergonomic solutions like lift tables, platforms, and other handling equipment is vital for allowing employees to execute their tasks without physical discomfort or injury risk. For large-scale industrial settings that handle substantial, weighty materials—especially outdoors—dedicated machinery such as cranes or reclaimers become indispensable components of any effective handling strategy.
Integrating Conveyors into Your Existing Workflow
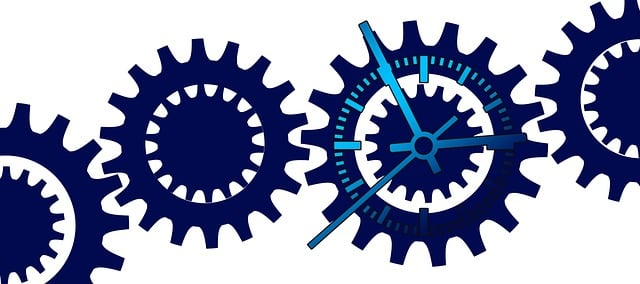
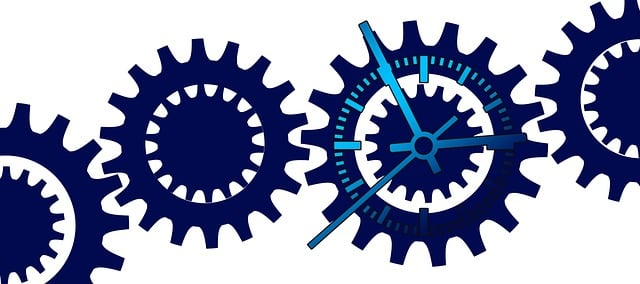
Incorporating a conveyor system into an established workflow demands meticulous attention to the nature of the material being handled, the space available for installation, and the objectives of operation. This strategic implementation is meant to augment existing procedures while resolving previous limitations and upkeep challenges, thereby facilitating a transition toward greater efficiency.
S. H. Fasteners can play a crucial role in this transition by providing their specialised knowledge. Help yourself guarantee that the selected conveyor solutions integrate flawlessly with present technological setups within your system.
Compatibility and Connectivity
Integrating conveyor systems effectively hinges on ensuring that compatibility and connectivity are prioritised. These custom-built systems seamlessly integrate into current operations, equipped with innovations such as lift gates and vertical transfer units to optimise workflow and guarantee a perfect physical integration.
At this juncture, the skill set of an experienced integration partner is crucial. They provide direction in aligning, programming, and setting up the conveyor systems to facilitate a seamless incorporation without interruptions or setbacks.
Minimising Downtime During Installation
Shifting to a different conveyor system requires careful management, especially since reducing downtime is critical. It’s essential to tackle environmental challenges like rust and corrosion head-on by implementing measures such as:
- Utilising zinc-plated or stainless steel chains for the conveyor, which act as barriers against corrosive elements.
- Constructing with strong welds on pins and bushes for longevity.
- Incorporating lightweight scrapers into the design.
- Emphasising the use of premium materials and precision in manufacturing processes.
These steps are key to guarantee that the system operates seamlessly right from the start, mitigating any chances of unexpected halts in operation.
Cost Considerations and Life Cycle Cost Analysis
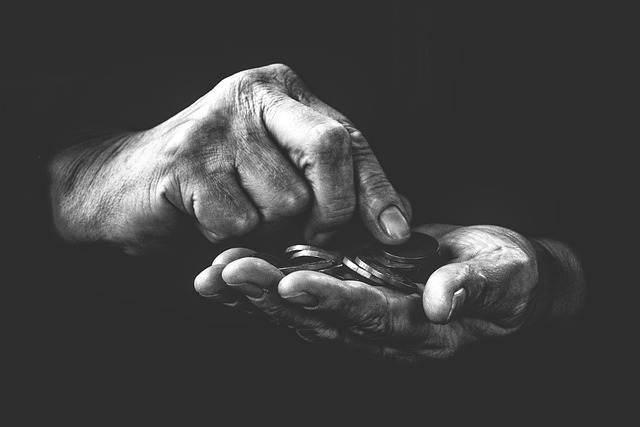
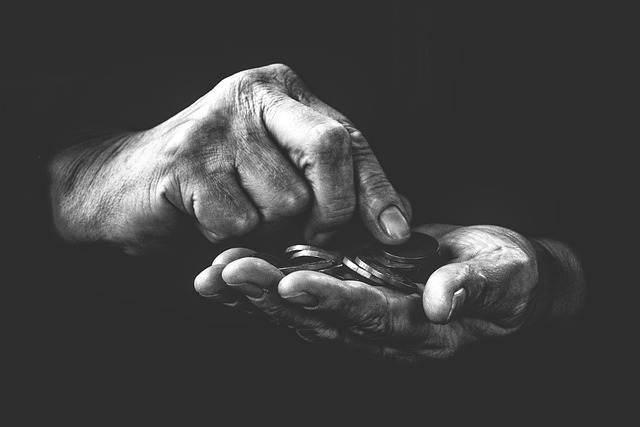
Opting to incorporate a conveyor system into operations is a major financial commitment. This encompasses not only the acquisition and setup expenses, but also custom engineering outlays, all of which are hefty. This investment goes into the future. The upfront costs as elements such as energy-efficient motors and smart control systems contribute to ongoing operational cost reductions.
Advanced automated systems, particularly those that feature retrieval capabilities with sophisticated sorting functions, can also lead to labor cost savings. These efficiencies serve to balance out the initial investment over an extended period, ultimately enhancing net profitability.
Evaluating Initial Investment


The procurement of a conveyor system starts with an assessment of the upfront costs. The evaluation should cover not only the purchase price of the equipment but also additional outlays, such as those for installation and necessary modifications.
For individuals apprehensive about immediate expenditures, alternatives like renting or leasing present a method to mitigate monetary strains while still obtaining the advantages offered by improved material handling.
You can also contact our comprehensive Customer Service representative to walk you through each step. We can better understand your needs and can help you navigate through this process.
Life Cycle Cost Benefits
Analysing the life cycle cost encompasses examining all ownership costs, including maintenance and operational expenses, alongside potential savings over time. Such analysis aids in decision-making by exposing the economic effects across a project’s duration.
Calculating the return on investment for conveyor systems involves assessing the gains obtained against upfront costs while considering reduced labor expenses, enhanced productivity, and decreased material damage and waste. Customisable conveyors offer unique benefits as they can be tailored to grow with your business needs, providing scalability that enhances overall returns—a critical advantage in the realm of material handling.
Enhancing Efficiency with Automated Conveyor Systems
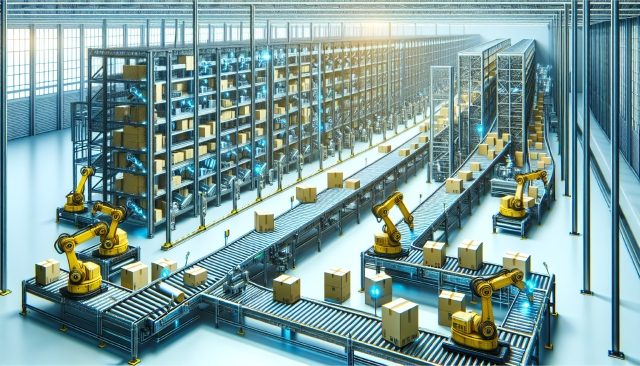
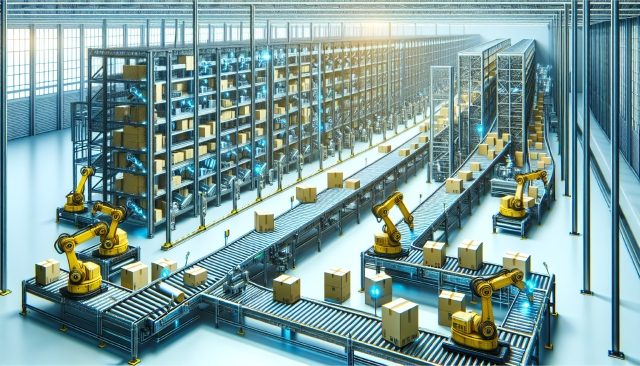
The introduction of automated conveyor systems has transformed the realm of material handling, optimising logistics and increasing efficiency. These systems have brought about numerous advantages by drastically minimising manual involvement.
- Decreased labor expenses
- Expedited and more precise order fulfilment
- Lessened physical burden on employees
- Removal of monotonous tasks
Potential Improvements
As a result, these improvements lead to a workforce that is both happier and more productive whilst optimising your operational costs. Human energy consumption can be heavily reduced.
Innovations in machine intelligence, robotics, and sensor technology have set the stage for advanced automation within material handling operations through state-of-the-art material handling equipment.
Automation Advantages
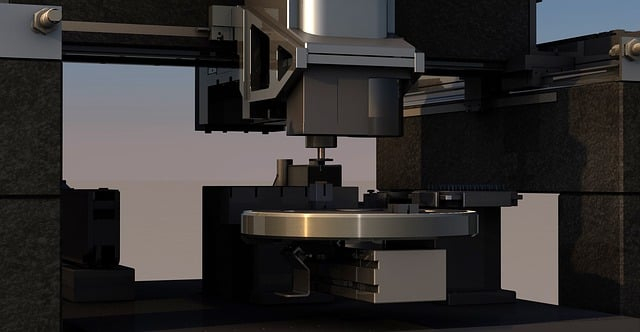
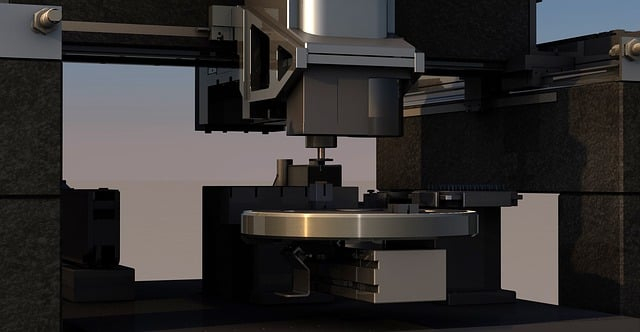
Conveyor systems have been revolutionised by automation, leading to uninterrupted workflows with significantly less downtime and the elimination of congestion often caused by the manual material handling of a human operator.
Specifically, sortation conveyors amplify operational efficiency through targeted delivery of products, freeing up employees for more skilled endeavours. Improvements in control technology and sensor precision facilitate meticulous monitoring and manipulation of materials—integrating seamlessly into current procedural operations.
Balancing Automation and Human Labor
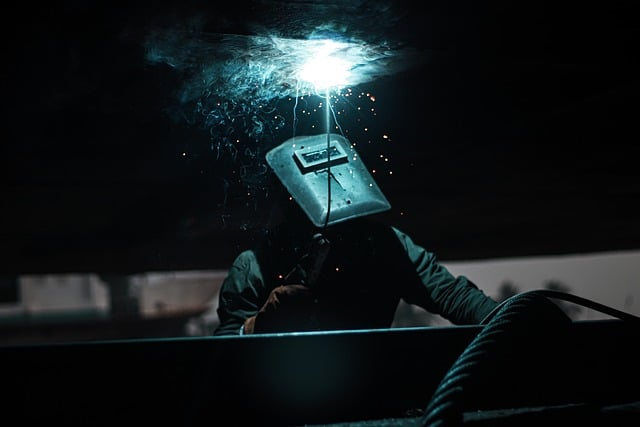
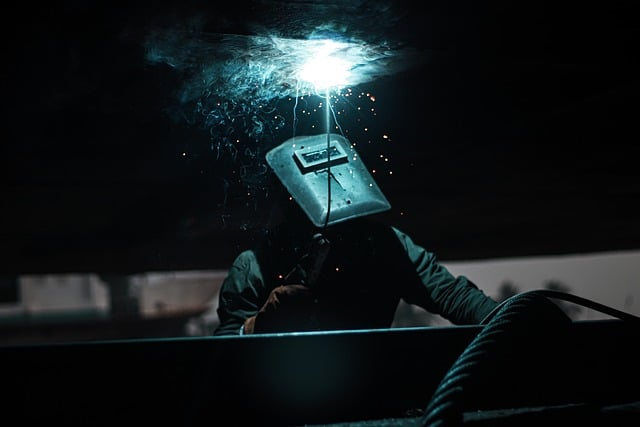
Automated equipment, despite its efficiency and accuracy in handling materials on conveyor systems, does not possess the versatility or rapid reassignment skills inherent to human workers. Finding equilibrium between mechanised operations and human labor is crucial.
It’s within this blend of human dexterity and machine precision where material handling processes reach peak efficiency. By leveraging the combined capabilities of humans and automated conveyors, a more effective workflow emerges.
Sortation systems can easily manage repetitive tasks and create in large quantities, however having human operator to manage the system will allow for specialisation and career growth.
Conveyor Maintenance and Upkeep
Maintaining the health of a conveyor system requires consistent attention to its upkeep and care. Ensuring that it is regularly cleaned to eliminate clogs, maintaining appropriate belt tension to avoid slipping, and implementing preventative actions to prevent breakdowns are all essential for the longevity and efficiency of the system. Neglecting these aspects can result in malfunctions that disrupt workflow. Thus, maintenance is not merely routine—it’s a crucial strategy for keeping the conveyor operational.
Routine Inspection and Servicing
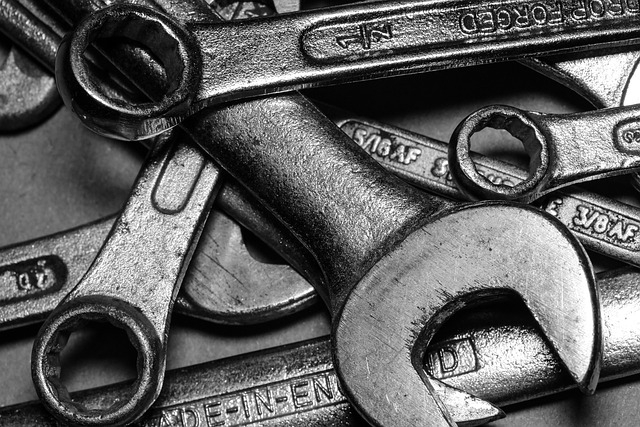
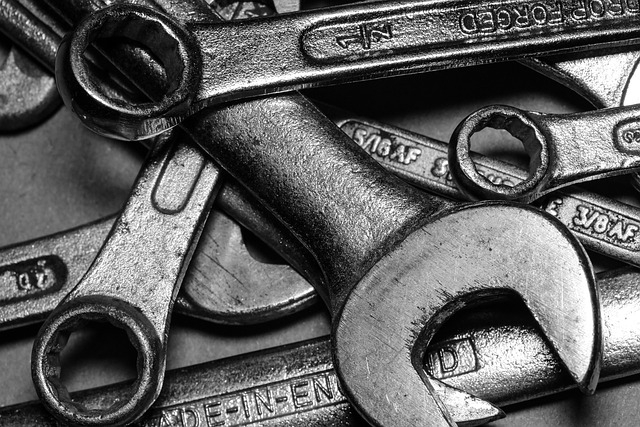
The essence of maintaining a conveyor system lies in consistent inspection and servicing. Daily maintenance tasks should encompass clearing away debris, conducting an assessment for unusual sounds, and monitoring for signs of belt slippage as well as any spillage of material. On a weekly to monthly basis, the focus shifts to the lubrication of bearings, examination of both belts and rollers within the conveyor, and replacement of components showing wear.
This annual care routine encompasses a thorough evaluation that includes checking the health of insulation lagging, motor performance, and e-stop system responsiveness to ensure they all operate correctly. Ongoing vigilance is also directed towards cleaning, scrutinising drive elements, and observing any deterioration on the surface of the conveyor belt. Both proactive and regular attention are critical for sustaining the uninterrupted operation of the conveyor system.
Responding to Wear and Tear
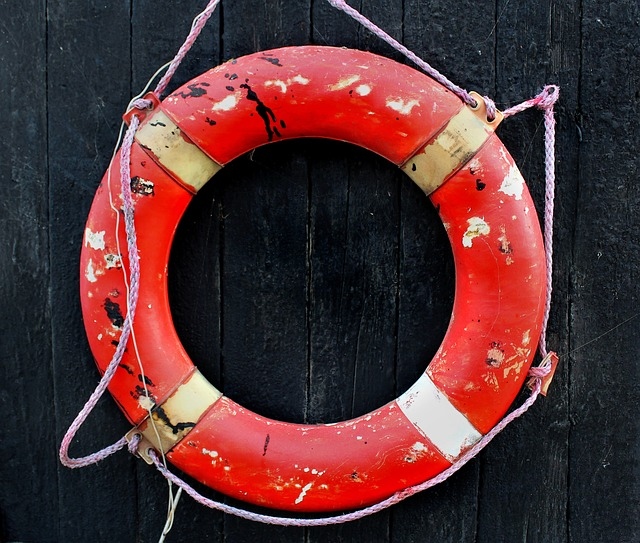
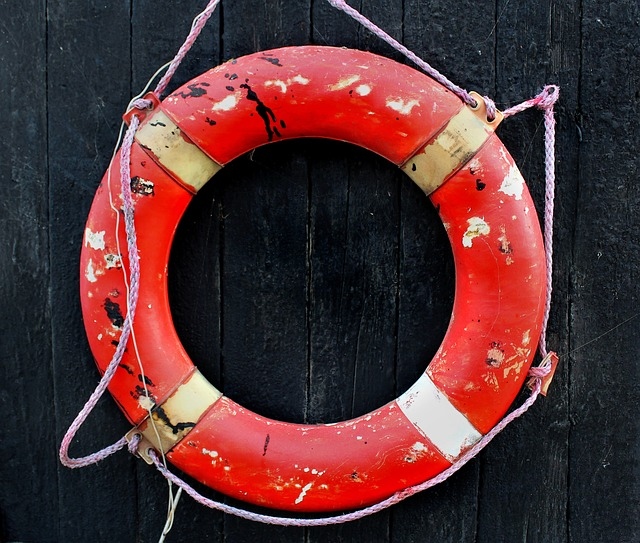
Ensuring the conveyor system’s integrity and functionality requires a proactive approach to managing wear and tear. By regularly conducting inspections, one can detect and repair components such as worn belts, which helps keep the system in prime working order.
It is crucial to replace parts like rollers and pulleys promptly to maintain smooth functioning within operations. Bearings play an essential role in minimising friction. Thus, maintaining them properly is imperative for extending the lifespan of the conveyor system while guaranteeing its continuous efficient performance.
Summary
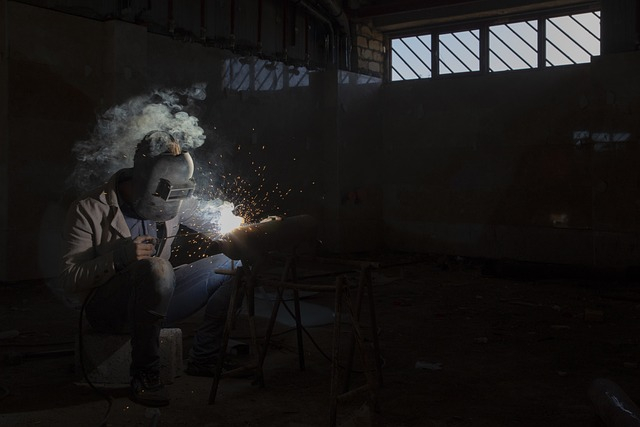
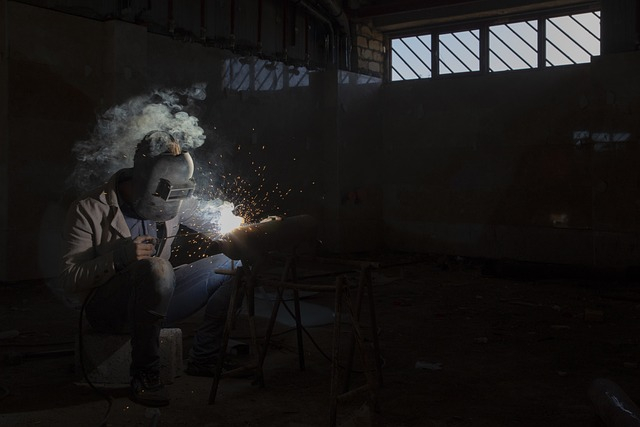
Embarking on the journey of enhancing material handling through efficient conveyor building services is a strategic endeavour that can transform the operational efficiency of any warehouse or distribution centre. From understanding the intricate components that make up these systems to integrating them seamlessly into existing workflows, the benefits of investing in conveyor solutions are clear. With careful consideration of cost, customisation, and maintenance, businesses can ensure a return on investment that extends well beyond the initial outlay. Let the power of well-designed conveyor systems carry your business towards a future of productivity and efficiency.
Frequently Asked Questions
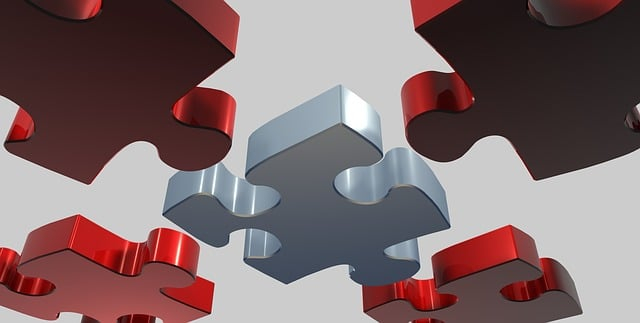
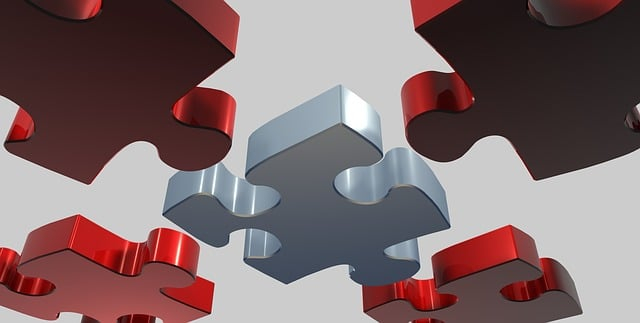
What are the different types of conveyor systems available for warehouse operations?
Warehouse operations utilise various conveyor systems, including transportation, accumulation, pallet, and gravity conveyors, to meet distinct material handling needs.
How can I ensure that a new conveyor system will fit into my existing workflow?
For a flawless integration of a new conveyor system into your established workflow, assess the current conveyor setup and collaborate with seasoned integration specialists or call our customer hotline for a personalised experience.
Are there cost-effective options for implementing conveyor systems?
Indeed, leasing or renting conveyor systems presents an economical solution for companies aiming to improve their material handling capabilities without the need for substantial initial capital expenditure.
How do automated conveyor systems enhance efficiency?
Conveyor systems that are automated optimise efficiency by smoothing out the flow of operations, cutting down on manual labor requirements, decreasing periods of inactivity, and delivering accurate handling of materials. This collectively leads to an improvement in overall operational effectiveness when it comes to material handling.
What routine maintenance should be performed on conveyor systems?
Ensuring that conveyor systems operate smoothly involves performing routine maintenance, such as eliminating accumulated debris and adequately lubricating the roller bearings. It is also critical to inspect belts and rollers for signs of damage, replace any components that show wear, and carry out comprehensive inspections annually to confirm all elements of the system function correctly.
Such maintenance practices are essential in averting malfunctions and guaranteeing that conveyor operations remain efficient.
How S. H. Chooi can help your specific needs
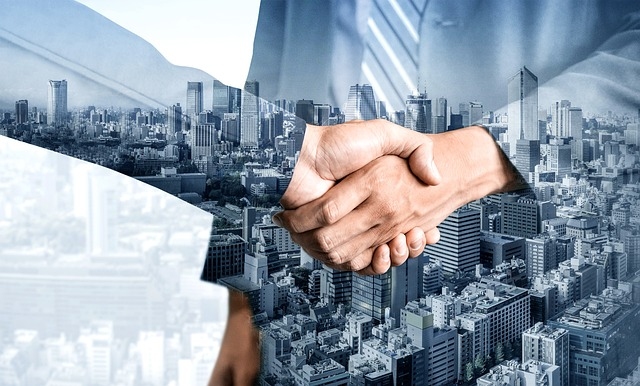
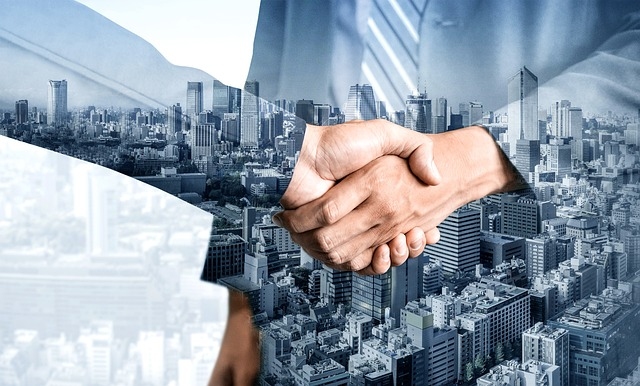
Services
- Dedicated Inventory Programs: S.H. Chooi offers tailored inventory programs designed to meet your specific needs, ensuring that you always have the right fasteners and materials on hand.
- Customised Precision Fasteners: We provide precision fasteners customised to your exact specifications, helping to streamline your inventory and reduce excess stock.
- Aluminium Profiles Structures and Line Building: Our comprehensive inventory includes aluminium profile structures and line building components, ensuring a one-stop solution for your assembly needs.
- Vendor Managed Inventory Systems (VMI): We implement VMI systems to manage your inventory levels efficiently, reducing stock-outs and overstock situations.
- Kanban Inventory Programs: Our Kanban programs facilitate just-in-time inventory management, enhancing workflow efficiency and minimising waste.
- Electronic Data Interchange (EDI): With EDI, we streamline communication and data exchange, ensuring accurate and timely inventory management.
- Ex-Works Pricing from our Penang Warehouse: All products are offered at ex-works prices directly from our warehouse in Penang, Malaysia, providing cost-effective solutions for your inventory needs.
- Comprehensive Customer Support: Our dedicated customer service team is always available to assist with inventory management inquiries and resolve any issues promptly, ensuring a seamless experience.
Conclusion
Trust us with your industrial needs!
Our customer service officers work tirelessly to answer all questions and resolve any issues efficiently and effectively. Use our customer service live chat, fill up the question form, or send us an email. You can also reach us by phone at +604 – 261 3001.